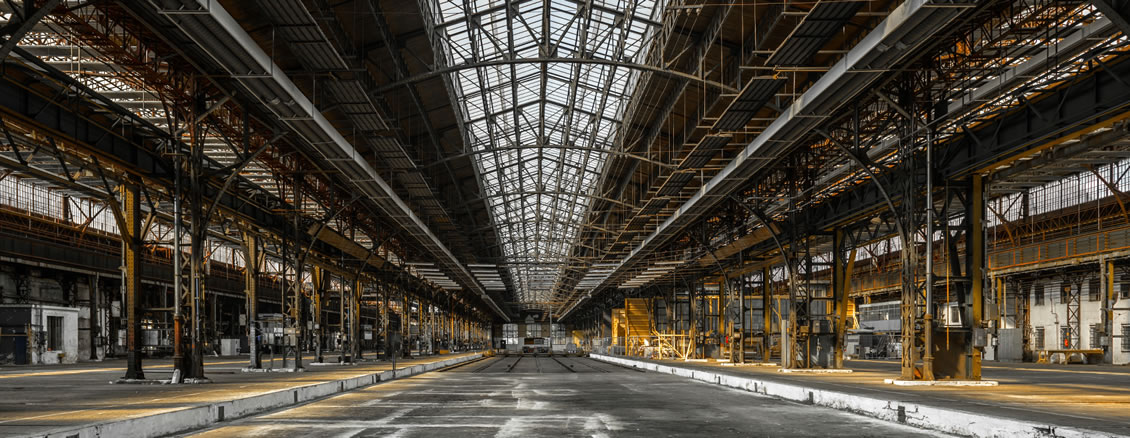
Time was that the machine operators on a manufacturing shop floor knew how many widgets to make by reading the work order off a piece of paper. Today, the typical manufacturing or distribution company has heavily-automated and computerized processes that tie into a backup office database.
Many companies have completely done away with the old work order packet and rely on computer technology to tell them what’s in their queue, what to work on next, and special instructions. Often, the paper trail is long gone.
The process goes a little something like this:
- The machine operators record their time and perform their own moves and other functions directly on the computer screen.
- The shipping/receiving department scans barcode or QR codes to receive and ship inventory.
This automation has increased productivity and improved tracking methodology, which has allowed manufacturing in economies with expensive labor forces to stay competitive with today’s world market. This shift has been good for manufacturing worldwide, improving conditions for the workers and predictability in delivering to the end customer.
There’s no denying the reliance on technology today and the need to build in resiliency, though it directly impacts your ability to recover.
What Happens after a Disaster?
Following a computer system failure, it’s not only hard to recreate the past, but it could also cripple your future.
If your production server goes down at 10 p.m. tonight, what’s the impact on the shop floor? For orders, shipping, receiving, purchasing, and planning? Immediately, you lose visibility into things like this, to name just a few:
- Where the parts are
- What’s in the queue
- How much you need to produce today
- Whether you need to order more resources
- Which order you’re working on
And that’s before you factor in the impact to Accounting and other parts of the business that are integrated across the company.
How Much Data Can You Afford to Lose?
Your recovery point objective or RPO is the maximum amount of data your business can stand to lose. Whether it’s orders, shipping, or receiving, without that filing cabinet of yellowing paper, how are you going to recover the data that was entered after your daily backup?
While you’re scrambling to reproduce your lost data—which might be minutes, hours, days, or never—the rest of your company is dealing with downtime, which is as expensive as it is disruptive. Some questions to consider as you calculate the cost of downtime include:
- Are you accounting for weighted machine rates or just personnel cost?
- How much are you including for missed or late shipments? (Opportunity costs are often higher.)
- What will your customers do when they can’t place an order electronically?
- How much are the late fees going to cost you? (Many manufacturers in the auto industry, for example, can be fined considerably for missing deadlines.)
How Can High Availability Help?
Some manufacturing and distribution companies say that they are not 24/7, so they don’t need high availability. This argument is only valid if you have paper backup, you don’t have fines for late shipments, your customers have no choice except to buy from you, and you have no regulations or IT audits to comply with. In other words, a highly unlikely combination.
Automation is essential for increasing productivity and getting the edge on your competitors. But you can’t ignore that it makes your business rely more heavily on the data in your systems to keep running smoothly. And it is important to keep your data redundant and highly available.
A high availability solution makes it possible for you to replicate your critical data to a backup server in real time, ensuring that your work orders are always ready for production and delivery, no matter if it rains or snows.
Get Started
If you’re like 45% of IBM i shops, you’re still pussyfooting along without a high availability (HA) solution, putting your business at risk. Don’t let budget or resources be your excuse for putting off HA one more day.